If you've ever peered behind the curtain at how things actually get made—whether it’s cars, sneakers, or circuit boards—you’ll bump up against two acronyms that sound suspiciously alike: MES and MOM. They’re tossed around like you’re magically supposed to know what each does. Spoiler: they’re not the same thing. Some plant managers still mix them up. Some software vendors like to blur the lines just to make sales. But here’s the twist—understanding the difference between these two can absolutely make or break the way a factory runs. There’s real money, efficiency, and even reputation on the line.
What is MES? Breaking Down Manufacturing Execution Systems
Let’s get straight to it: MES stands for Manufacturing Execution System. This is the digital nerve center tracking all those little manufacturing steps that turn raw stuff into a finished product. If you walk into a plant and see giant screens with real-time data about which machines are running, which operators are on shift, and how many goods rolled off the line today—that’s MES at work.
Picture MES as your control tower. It connects to machines, sensors, and people. It collects bursts of data about temperature, pressure, machine speed, even which worker was at which workstation. Need to know why a batch failed yesterday at 3:17 p.m.? MES can probably show you who pushed the button and what the machine settings were. That level of visibility is gold in manufacturing, where catching mistakes early saves thousands—or millions—of dollars.
But MES does more than record-keeping. It controls the workflow on the shop floor. The system issues work orders, tells workers what instructions to follow, logs test results, and even tracks inventory levels. If parts are running low on Line 4, MES triggers an alert. It keeps everything humming and finds the weak spots before they turn into angry customer complaints or expensive recalls.
According to one 2024 study from Gartner, companies using MES reduce unplanned downtime by over 35% and can boost output by as much as 19%. And since MES sends real-time data up to management, it makes audits a breeze and supports decision-making with hard numbers, not just gut feel.
Still, MES isn’t a magic bullet. Without good data or the right setup, it’s just a fancy dashboard. Installation and integration take time, money, patience—and usually a dedicated IT or automation team. But the benefits stick around for the long haul, especially for companies chasing ISO certifications or worried about traceability regulations.
What is MOM? Decoding Manufacturing Operations Management
Now, let’s untangle MOM—Manufacturing Operations Management. This isn’t a single system or piece of software. It’s a bigger picture approach: imagine it as the playbook for how an entire manufacturing operation gets planned, executed, monitored, and improved.
MOM covers everything from production scheduling to quality control, maintenance, inventory, and even compliance. You can think of it as the brains orchestrating manufacturing at every level—from what's happening on that factory line right now up to the monthly executive dashboard. If MES is the engine running your car, MOM is the navigation system plotting the fastest route, suggesting pit stops, checking tire pressure, and warning you about speed traps ahead.
MOM systems usually include MES as one of their modules, but they stretch much wider. You may see MOM platforms managing R&D workflows, recipe and formula management for food or chemicals, process improvement tools, or advanced analytics dashboards that crunch historical data for deep insights.
A survey from ARC Advisory Group in 2023 found that manufacturers using a full MOM strategy saw product quality complaints drop by 22% in a single year and on-time delivery rise by almost 15%. Why? Because MOM systems connect the dots between planning, execution, logistics, and customer needs—not just what’s happening right now, but how to get better next time.
Implementing MOM means more than just buying software. It can shake up company culture by forcing engineers, planners, machine operators, and quality managers to collaborate on shared data. Some companies even appoint a dedicated ‘MOM champion’ to break down silos and show teams how their daily tasks link to the bottom line.
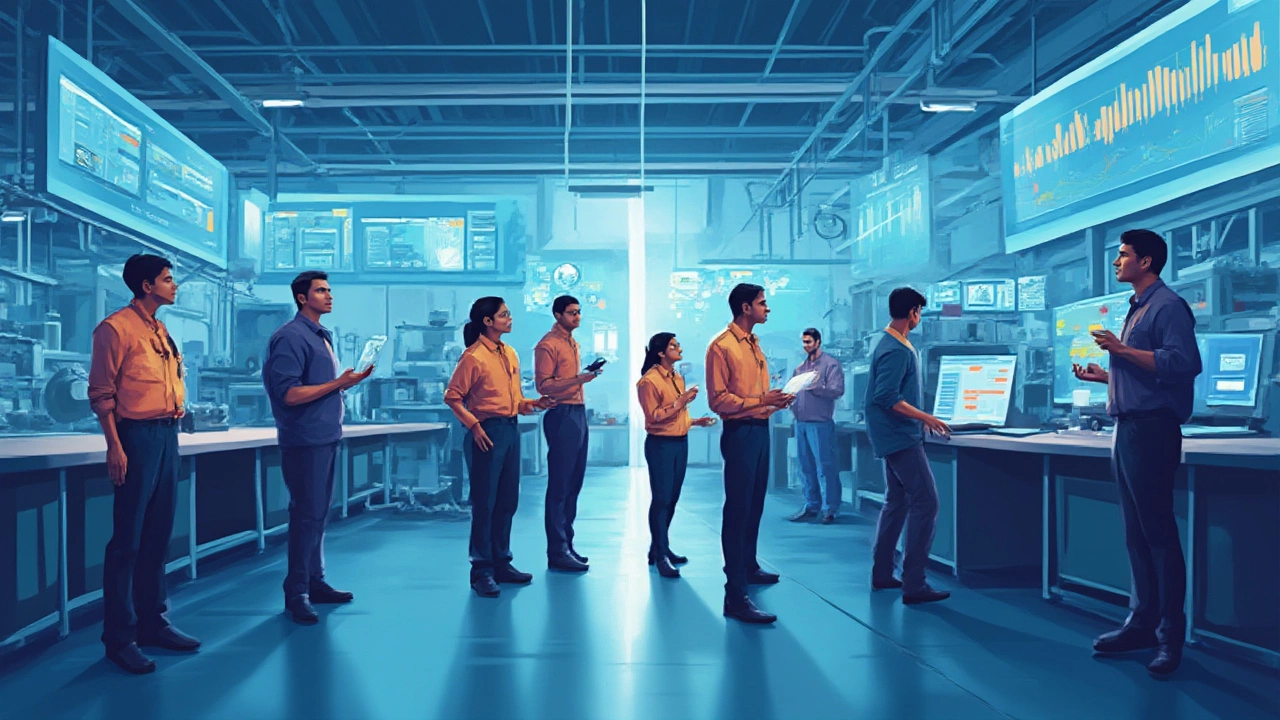
Key Differences: MES vs MOM Face-Off
Here’s where things get interesting. MES and MOM aren’t mutually exclusive. In fact, a healthy manufacturing company probably needs both. But the devil’s in the details—MES handles execution; MOM manages the whole operation. Let’s lock in on what sets them apart.
- Scope: MES focuses on real-time, on-the-ground production tasks—think one shop floor or factory. MOM covers the entire operation, from planning through delivery and continuous improvement across companies or sites.
- Function: MES is about tracking, documenting, and controlling manufacturing processes. MOM is about process optimization, advanced analytics, performance management, and making sure every department is rowing in the same direction.
- Modules: MES typically includes work order management, traceability, performance analytics, shop-floor scheduling, and machine data capture. MOM folds in MES and layers on R&D management, supply chain integration, quality systems, and even regulatory compliance management.
Check out this simple side-by-side table to spot the main differences:
MES | MOM | |
---|---|---|
Focus | Shop floor operations | All manufacturing operations |
Primary Goal | Execution & real-time control | Optimization & management |
Scope | Single plant/floor | Multiple processes/sites |
Components | Production, tracking, quality | MES + supply chain, R&D, analytics |
Data Depth | Real-time, detailed events | Historical, analytics-driven |
If you just need precise control and data for today’s shifts, MES delivers. But if you want big-picture insights and cross-team alignment, MOM brings the whole operation together.
Choosing the Right Solution: What Manufacturers Need to Know
Walking into an MES or MOM project without a plan is like building a house with no blueprint. First, figure out your biggest headaches. Do you mostly struggle with machine downtime, or are you constantly chasing paperwork for audits? Maybe your teams are working in silos—sales blaming production, production blaming supply chain. A strong MOM approach pulls everybody onto the same page with shared goals and data.
Small to mid-sized factories sometimes start with MES, because it solves their immediate pain points: downtime, traceability, and production control. But as you grow, those production lines start overlapping with warehousing, logistics, customer service, and even R&D; that’s when MOM starts to shine. If you sell to industries like automotive or pharmaceuticals, traceability and compliance mean MES is non-negotiable from day one. But to join the top-performing digital factories, you need MOM’s broader structure to break down data islands and create a culture of continuous improvement.
Here are some questions to help decide what’s right for you:
- Are your problems mostly on the factory floor (equipment performance, production bottlenecks)? Then start with MES.
- Do you need to tie together quality, maintenance, supply chain, and inventory? MOM is probably the better fit.
- Is your company operating multiple sites or expanding quickly? MOM platforms can unify scattered data and teams.
- Are regulatory compliance and product genealogy critical? MES will be essential, but MOM makes audits much easier.
Another tip: Watch out for vendors that promise an “all-in-one” MES/MOM solution. Dig into their modules, ask exactly what’s included, and talk to real users—not just the sales team. There’s no ‘best’ solution for everyone; sometimes, a hybrid approach using both MES and MOM delivers the most value. And don’t forget change management—getting shop floor workers and managers excited (or at least on board) might be your biggest challenge.
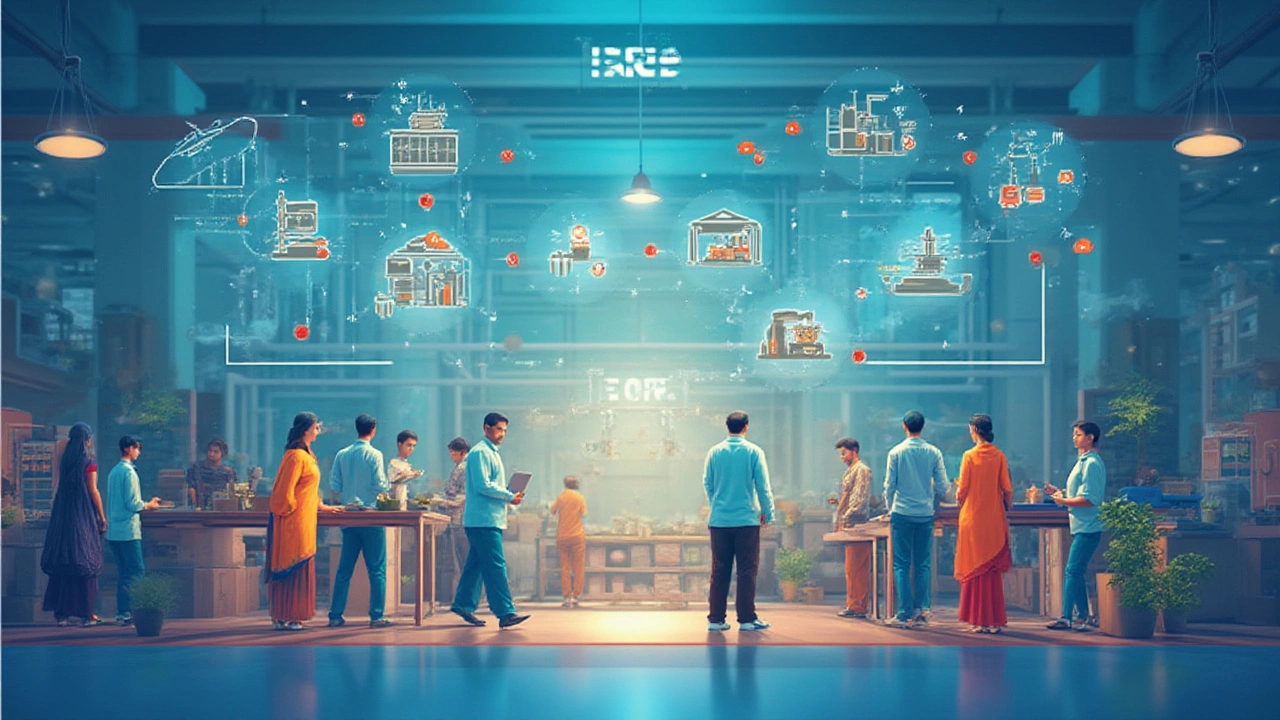
MES and MOM in Action: Real-Life Impact and Future Trends
The last few years have kicked digital transformation into high gear. There’s a smart factory boom all around the world, and it’s not slowing down. According to Deloitte’s 2025 Manufacturing Outlook, 65% of manufacturers are increasing investment in MES, MOM, or both, chasing better productivity and fighting off supply chain shocks.
Let’s talk real-world impact. One European food manufacturer used MES to track batches and instantly trace allergens—a game changer when a supplier flagged a contamination. Instead of a total recall, they pinpointed the one shift and batch at risk, saving millions. Meanwhile, a global electronics giant leaned into MOM to unify its MES, quality control, and asset maintenance across 12 factories on three continents. That cut average time-to-market by over a month—enough to outpace several competitors.
The real magic comes from connecting MES data (think: temperature at time of assembly) with MOM analytics (think: trending defect rates by week and team). It’s like watching an NFL replay with all the camera angles, not just one. You see patterns, causes, and improvement ideas you’d never spot working in isolation.
Where is this all heading? Smart factories will keep blurring the lines between MES and MOM. With AI now analyzing production data for predictive maintenance, digital twins simulating operations before launch, and cloud-based platforms letting managers monitor multiple global sites, the boundaries keep shifting. Expect more open, modular solutions—and more pressure on companies to sync not just shop floors, but the whole business, in real time.
So yes, it’s easy to get confused with MES and MOM, but pretend they’re just buzzwords and you’ll miss a huge opportunity. These systems aren’t just IT upgrades; they’re the backbone of the world’s most competitive manufacturing teams. Choose wisely, and you’ll see better products, happier customers, and less stress all around. Who wouldn’t want that?