Manufacturing today isn't just about churning out products. There's a whole web of factors that determine whether a company sinks or swims. From high-tech machinery to savvy government policies, understanding these components is key to thriving in the industrial world.
First up, technology. It's no longer a nice-to-have; it's a must-have. Machines are getting smarter, and companies that aren't keeping up are at risk of falling behind. We're talking robots that do the heavy lifting and AI systems that boost production efficiency. But all these gizmos are nothing without the skills to run them.
This brings us to the next critical factor: a skilled workforce. Manufacturing isn't just manual labor anymore. Workers need a mix of tech know-how and adaptability to manage changing production needs. That's why investment in training and development is crucial. Plus, there's always the supply chain and logistics puzzle to solve...
- The Role of Technology in Manufacturing
- Skilled Workforce and Training
- Supply Chain and Logistics
- Government Schemes and Policies
- Sustainability in Manufacturing
- Quality Control and Innovation
The Role of Technology in Manufacturing
It's no secret that technology is reshaping the manufacturing landscape. From faster production lines to safer work environments, the input of tech advancements is hard to ignore. Manufacturing factors that rely heavily on technology are those that can adapt and innovate the quickest.
Automation continues to be a game-changer, with smart robots and machines decreasing human error and boosting efficiency. Manufacturers are now employing cobots, which are designed to work alongside humans, performing tasks that require precision. Isn't that cool? Not only does this enhance production speed, but it also leads to huge savings on labor costs.
Besides robots, data analytics is a big deal. By analyzing big data, manufacturers can predict equipment failures before they happen, optimize supply chains, and even personalize products to suit market demands. This not only saves time but also resources, which is vital in staying competitive.
Let’s not forget about the Internet of Things (IoT). It’s making it possible to connect all parts of the production process. Machines 'talk' to each other, share vital stats, and even schedule their own maintenance checks. Technological advancements like these ensure that factories run smoothly with minimal downtime.
Industry 4.0 is here, bringing smarter, more efficient production processes. With the integration of AI and machine learning, plants can adapt to changes in real-time, enhancing overall productivity. In New Zealand, we've seen a sharp rise in factories adopting these technologies, leading to a surge in manufacturing output.
While the initial investment in technology may seem steep, the long-term benefits of reduced operational costs and increased output can't be overstated. As the tech landscape continues to evolve, those who embrace these changes will likely lead the pack in the ever-competitive manufacturing sector.
Skilled Workforce and Training
In the world of manufacturing, having a skilled workforce is like having the right ingredients for a great meal. You can't just rely on machines and technology; you need people who know how to use them effectively. This means investing in training and education to keep pace with all the tech advancements.
Many manufacturing companies are partnering with local colleges and trade schools to create tailored training programs. These programs focus on equipping workers with the necessary skills for operating modern machinery, managing production lines, and even understanding complex data systems. By doing so, they're not just filling jobs—they're setting up employees for long-term success and growth.
Moreover, government schemes are stepping up to support these initiatives. For instance, some regions offer grants or tax incentives to companies that provide upskilling opportunities for their employees. This is a win-win, as businesses boost their capabilities while workers enhance their skill sets.
Here's a neat stat: According to a study, companies that introduce robust training programs see a 20% increase in productivity within the first year. That's a huge deal in today's competitive market. Encouraging ongoing learning isn't just good for morale; it's essential for keeping up with rapid changes in production efficiency.
Keeping skills up to date also means embracing innovation. The days of routine, unchanging processes are over. Being adaptable is critical, and having a team that can pivot quickly thanks to continuous learning makes all the difference. At the end of the day, a company is only as strong as its team, and investing in people is investing in future success.
Supply Chain and Logistics
Supply chain and logistics are at the heart of production efficiency. Think of it as the network that ensures raw materials arrive on time and finished products reach their destinations without a hitch. Today, with the global economy tightly interlinked, a snag in the supply chain can throw a giant wrench into the works.
In manufacturing, minimizing disruptions means everything. Imagine your assembly line grinding to a halt just because a shipment got delayed. Not fun, right? That’s why companies are investing big time in supply chain technologies. These tools help track everything from inventory levels to real-time delivery status. The goal is to be proactive rather than reactive.
One tool that's been a game-changer is predictive analytics. By using data from past trends and current conditions, manufacturers can forecast demand and adjust their supply chains to match. This reduces overproduction and waste, saving both time and money.
Logistics, on the other hand, is all about movement and storage. Efficient logistics can be a real money-saver. Many companies are now using automated warehouses, which streamline the storage and retrieval process, cutting down on labor costs and human error.
Let's not forget the role of government schemes. Policies that reduce transport taxes or subsidies for new tech investments can significantly ease the logistical burden. These initiatives help manufacturers boost their industrial growth, making the journey from raw material to the consumer as smooth as possible.
Here's an interesting nugget of info: Companies that integrate supply chain management software see up to a 15% increase in efficiency, according to industry reports. That's a significant advantage in our fast-paced world!
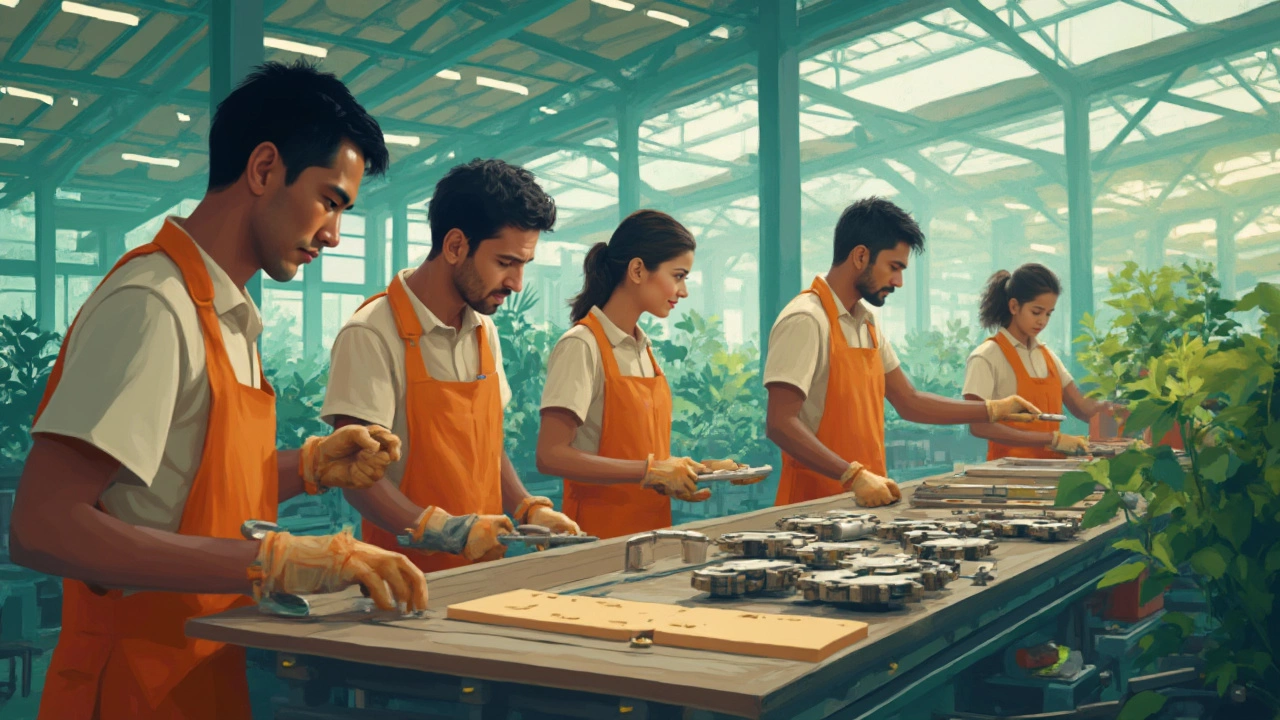
Government Schemes and Policies
When it comes to manufacturing, government schemes can be a real game-changer. In many countries, these policies are designed to bolster industrial growth and ensure businesses don't just survive but thrive.
Let's take a look at some standout examples. In New Zealand, the government has launched initiatives like the 'Regional Growth Programme' which aims to drive economic development by supporting local industries. This program offers funding and resources for businesses willing to expand and innovate.
Across the pond in Australia, the 'Advanced Manufacturing Growth Fund' plays a significant role. It provides grants to industries willing to invest in advanced technologies or strategies improving production. And of course, in the US, the Manufacturing Extension Partnership (MEP) supports small and medium-sized manufacturers with advice, support, and resources made easily available.
These schemes aren't just limited to funding, though. They cover tax incentives, reduced regulations for startups, and even training programs that encourage small businesses to up-skill their workforce without extra financial strain.
Here's a quick look at some impactful government policies:
- Tax Incentives: Programs like reduced corporate tax rates for manufacturing firms stimulate investments in new technology.
- Training Grants: Designed to help businesses skill up or retrain their workforce to meet the demands of the modern manufacturing landscape.
- Regulatory Easing: Simplifying the rules for new businesses helps startups focus more on growth and less on bureaucracy.
And, if you're curious about how effective these schemes can be, let's consider that in New Zealand alone, government-supported manufacturing initiatives contributed to a 3% GDP growth in 2023. That's some serious potential unlocked.
Sustainability in Manufacturing
Sustainability isn't just a buzzword; it's becoming the heart of modern manufacturing. With the planet's resources depleting faster than ever, companies are feeling the pressure to produce goods while keeping the Earth's well-being in mind. But what does sustainable manufacturing actually look like?
Well, it starts with using renewable energy. Many factories are ditching fossil fuels for greener options like solar and wind. Making this switch not only helps save the environment but also reduces long-term costs. Plus, big brands are jumping on the bandwagon. BMW, for instance, powers its Leipzig plant entirely with on-site wind turbines.
"Sustainability is no longer about doing less harm. It’s about doing more good." – Jochen Zeitz, Chairman of Harley-Davidson
Another key piece of the sustainability puzzle is waste reduction. Think less garbage, more recycling. Factories are cutting down on waste by reusing materials and adopting circular economy principles. It's all about finding ways to give products a second life rather than tossing them into a landfill.
Then there’s water usage. Manufacturing can be a thirsty business, but smart factories are finding ways to cut back. For instance, they’re installing systems to recycle water within the plant, reducing the need for fresh water intake.
- Energy efficiency: Upgrading old machinery and lighting to energy-efficient models.
- Recycling programs: Setting up processes to recycle materials, reducing waste.
- Local sourcing: Using local materials to cut down on transportation emissions.
- Employee engagement: Training workers to understand and participate in sustainability goals.
Let’s not forget about government schemes. They can be a huge help, offering incentives for companies that make the effort to go green. In some places, governments provide tax breaks or grants for upgrading to more sustainable technologies.
By focusing on sustainability in manufacturing, companies can not only help the planet but also appeal to eco-conscious consumers. In 2024, a study found that 67% of people prefer to buy from brands that show they care about the environment. With stats like these, it’s clear that going green is not just an ethical choice, but a smart business move too.
Quality Control and Innovation
Keeping tabs on quality control and sticking with innovation is like the secret sauce for success in manufacturing. Why? Because nothing takes down a brand faster than a dud product.
A huge part of making sure products hit the mark is having a rock-solid quality control system. With consumers expecting more bang for their buck, the pressure is on to deliver top-notch goods. Using cutting-edge tech like AI-driven inspections can help spot issues before they turn into disasters.
And hey, quality control isn't just about catching mistakes. It's about making processes smoother and more efficient. Investing in quality doesn't just keep customers happy; it saves money in the long run by reducing mistakes and returns.
Let's not forget innovation. It's about keeping the product lineup fresh and exciting. Innovation fuels growth. It’s the difference between setting trends and playing catch-up. Whether it’s tweaking a current product or launching something totally new, the goal is to solve real problems for real people.
Manufacturers that stick to tried-and-true methods risk becoming irrelevant. The magic happens when quality and innovation work hand-in-hand. Imagine businesses boosting their brand reputation one solid product at a time, while also shaking up the market with cool new offerings.
- Regularly revisit your quality check systems and update them with the latest tech.
- Keep a dedicated team focused on brainstorming and developing new ideas.
- Gather feedback from customers to direct innovation efforts effectively.
So, to wrap it up, embracing strong quality control practices while pushing for ongoing innovation can set manufacturers up for solid success. It's all about finding that sweet spot where efficiency and creativity meet.