Think manufacturing in India should be booming by now? You're not alone. Every year, the government launches fresh schemes for 'Make in India', big companies promise new factories, and reports boast about growth potential. Yet, if you talk to anyone in chemical manufacturing, you hear a different story—permit headaches, delays, and endless back-and-forth with government offices.
Here's the thing: the chemical sector is huge for India's economy, making up about 7% of the country’s GDP. But getting a new plant running? It’s like running an obstacle course blindfolded. From environmental clearances that can drag on for years, to outdated transport routes that make moving raw material a nightmare, progress stalls at every step. It's little wonder many companies, big and small, feel stuck while neighboring countries zoom ahead.
- Red Tape and Regulations
- Supply Chain and Infrastructure Woes
- Skills Gap and Worker Shortages
- What Chemical Manufacturers Can Actually Do
Red Tape and Regulations
If you ask someone in manufacturing India why they’re frustrated, the answer usually starts with paperwork. In chemical manufacturing, every new project needs a mountain of permits and NOCs (No Objection Certificates) from at least half a dozen agencies. Environmental clearance alone can take anywhere from 12 to 36 months, and you never know if things will suddenly stall because of a missing document.
The rules change often, and they're rarely simple. Chemical manufacturers in India have to deal with overlapping mandates from the Ministry of Environment, Pollution Control Boards, state governments, and sometimes, even the local gram panchayat. The same factory that gets the green light from one office can get stuck in another due to slightly different interpretations of the rulebook. It's exhausting for both big industry names and small startups.
Here’s a look at how long some of these approvals can take on average:
Approval Type | Average Waiting Time |
---|---|
Environmental Clearance | 12 - 36 months |
Land Allotment | 6 - 12 months |
Pollution Board Approval | 4 - 8 months |
Factory License | 2 - 6 months |
It's not just the time. Sometimes the bribes expected for quick processing can make costs spiral, and smaller companies often just can't afford to play the game. One well-known example is the time it took a major international chemical company five years to get their Mumbai plant running because of dozens of regulatory delays.
If you’re a newcomer to chemical manufacturing India, here’s what the paperwork maze looks like:
- Apply for land and building permits from state development authorities.
- Get environmental clearances at both state and central levels.
- Obtain safety and pollution board approvals, which may involve multiple site visits.
- Coordinate with labor departments for workforce and welfare licenses.
- Repeat documents and verifications at almost every new office.
The government occasionally promises faster 'single window clearances,' but most chemical manufacturers say these windows are rarely open or actually single. Until the system genuinely streamlines, red tape is going to keep slowing things down for chemical manufacturers India trying to get off the ground.
Supply Chain and Infrastructure Woes
The manufacturing India scene, especially for chemical manufacturers India, runs into trouble when it comes to roads, rail, ports, and the raw basics of moving things around. For example, only about 40% of India's highways are considered in decent shape for heavy truck loads. Freight that should move in a day can sometimes take three. For chemicals, which are time-sensitive and need careful handling, that is a real headache.
Ports aren’t much better. Jawaharlal Nehru Port, which handles a chunk of India’s container traffic, regularly faces congestion. Ships end up waiting, sometimes for days, to load or unload. Now, compare this to ports in Vietnam or China, where operations run almost like clockwork—it’s clear where the hold-up is.
Along with slow movement, there's the problem of unpredictable power cuts. Chemical plants run 24/7 and even half an hour of power loss can throw production into chaos. Backup generators are common, but they drive up costs fast. And there are cost issues everywhere—exporters in India often pay more in logistics than those in Malaysia or Thailand, by about 20-30% on some routes.
Country | Average Inland Logistics Cost (USD/ton) | Avg. Port Dwell Time (days) |
---|---|---|
India | 90 | 5 |
Vietnam | 60 | 2 |
China | 55 | 1.5 |
There are fixes in progress—like the new dedicated freight corridors and Digital India efforts—but they haven't yet changed the daily slog for most chemical factories. If you run a manufacturing unit here, the tip is to lock in reliable transport partners and invest in real-time tracking tools. It won’t fix the roads, but you’ll at least know exactly where your shipments are stuck and for how long.
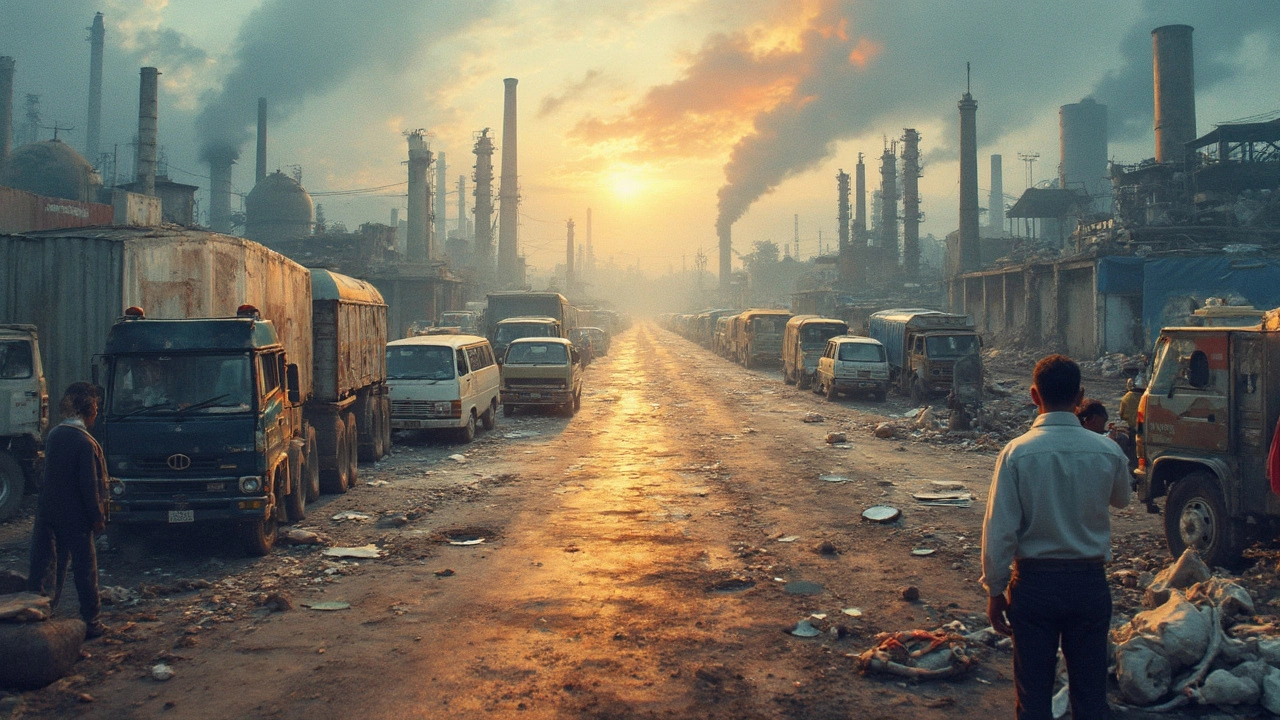
Skills Gap and Worker Shortages
Walk into any decent-sized chemical manufacturers India facility, and someone will tell you about their struggle to find people who actually know what they’re doing. Sure, India’s got a huge population, but the truth is, trained workers with the right technical know-how are hard to come by. Chemical manufacturing isn’t just about mixing stuff—it’s about safety protocols, handling hazardous materials, running advanced machinery, and meeting global quality standards.
Here’s something wild: a 2023 survey by the Indian Chemical Council found that almost 60% of chemical companies believe the shortage of skilled talent is their #1 headache. That’s a big deal when you consider how many steps in production need experienced hands-on workers, not just untrained laborers fresh out of school.
Why’s the gap so wide? For starters, most colleges and technical institutes focus on theory—when new grads walk onto the factory floor, they’re lost. There aren’t enough vocational programs that train people on what the industry really needs. On top of that, automation is taking over boring or dangerous jobs, raising the bar even higher for what skills you actually need to stay employed in this sector.
Manufacturing India companies are feeling the pinch. Many have to spend extra time and money retraining new hires or even fly in experts from abroad to sort things out. Some local plants run at reduced capacity, not because there’s no demand, but because there’s nobody to run the machines safely.
Check out this data from the National Skill Development Corporation:
Job Role | Vacancy Rate (%) | Comments |
---|---|---|
Process Technician | 28 | Lack of hands-on skill |
Quality Control Chemist | 23 | Few practical training programs |
Plant Engineer | 35 | High demand, low supply |
What can chemical companies do right now? A few tips that actually work:
- Set up in-house training labs where new workers can learn by actually doing the job, not just reading about it.
- Partner with local colleges and offer internships or apprenticeships—real work experience beats theory every time.
- Bring in senior industry pros as mentors to coach new hires. Small teams with a mix of old hands and fresh faces work best.
If this skills gap doesn’t get fixed soon, Indian industry growth will keep running into a wall, especially in the fast-moving chemical sector.
What Chemical Manufacturers Can Actually Do
It might feel like the system is stacked against you, but there are things chemical manufacturers India can actually control. Start with efficiency—streamline your production so you cut waste and save money. It isn't only about shiny new machines. Sometimes, small tweaks in how staff handle materials or how batches are scheduled make a visible difference.
Next, work your network. The best chemical manufacturers India often join industry groups like the Indian Chemical Council. This gives you better access to updates on regulatory changes and a voice when policies are written. And don’t sleep on digital: adopting even simple supply chain management software can shrink those annoying delays in procurement and shipping. According to a 2023 Confederation of Indian Industry report, plants using real-time inventory tools cut delivery times by up to 18%.
Strategy | Potential Benefit |
---|---|
Switch to local suppliers | Reduces risk of import hold-ups |
Implement basic automation | Boosts output, slashes manual errors |
Invest in worker training | Handles skills gap, improves safety |
Lobbying still matters. Get involved with trade associations pushing for simpler clearances and cleaner policies. As Sunil Kumar of the Indian Chemical Council put it,
"Regulatory transparency and genuine ease of doing business can turn India into a global hub, but the push has to come both from policy makers and the industry itself."
Above all, never stop learning from others—in India or outside. Track what’s working in Thailand and Vietnam when it comes to eco-friendly practices or logistics. Sometimes, that means reaching out directly to peers online or attending hands-on workshops when regulations change. There's no silver bullet, but quick wins add up—especially when big policy overhauls move at a snail’s pace.